RADIFOCUS™ Guide Wire M celebrates its 40th anniversary in 2025. We spoke with three associates who work with this legacy product to learn about their efforts to maintain quality while ensuring stable supply, and their personal connection to this product.
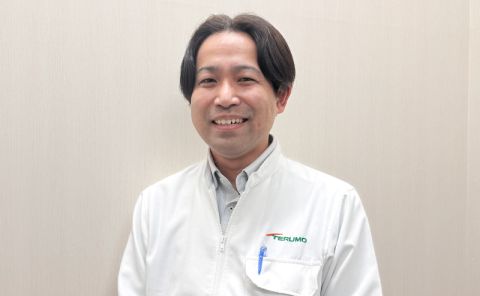
Daisuke Mochiyama
Manager
TIS Production GW Section
Ashitaka Factory
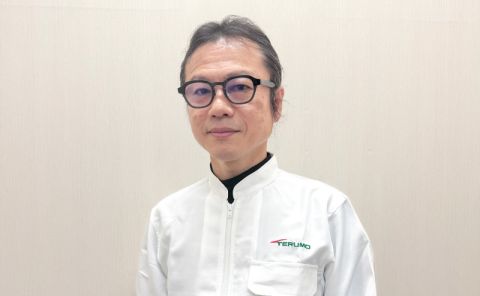
Noriyuki Tamai
Senior Engineer
Ashitaka Factory
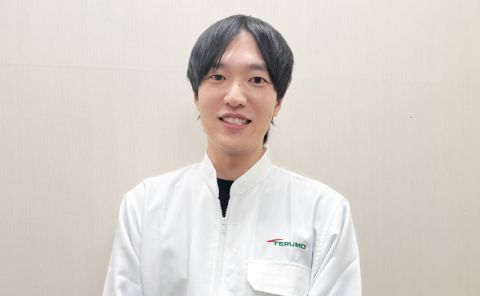
Yuichi Ishiwata
Research Engineer
Ashitaka Factory
- RADIFOCUS™ Guide Wire M has been used in clinical settings for many years.
What do you see as its strengths?
Daisuke Mochiyama (DM): I’d say how it’s continuously increased production since launch while maintaining consistent quality levels: the product delivers the same reliable performance every time. What we call kinshitsu, really captures this approach.
Noriyuki Tamai (NT): In how even after 40 years, demand continues to grow. It's rare to find a product with such enduring clinical value.
Yuichi Ishiwata (YI): For me it's the comprehensive performance and trust we've built. The broad lineup means it can be relied on across various clinical situations. The fact that it's been used in clinical practice for so long shows we're meeting the usability and performance standards that matter. This established trust is what makes our guidewire special.
- Given this product's long history, you might think there's nothing left to improve. Is that the case?
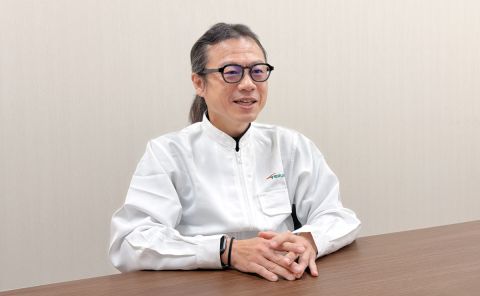
NT: In development, we're continuously addressing increasingly strict regulations that accompany healthcare advancement, ensuring our product design remains compliant.
RADIFOCUS™ Guide Wire M was launched before many current country-specific regulations existed. The product design has remained virtually unchanged since its creation 40 years ago. However, as new regulations continue to be implemented, we need to ensure ongoing compliance.
- But the product itself remains the same?
NT: Exactly. The product is unchanged, but we’re constantly adapting to meet annually updated regulatory and quality requirements.
YI: We now consider far more clinical scenarios and challenging situations compared to when it was originally launched, collecting and verifying all the data before release.
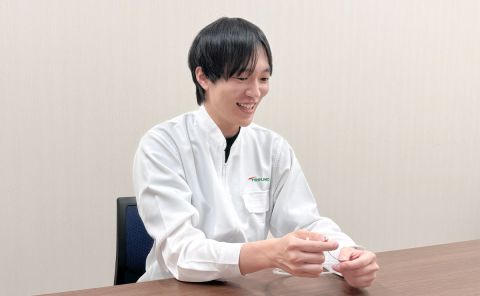
From a quality assurance standpoint, we’re continuously refining and evolving our approach. As part of our responsibility in development, we work closely with our quality assurance teams to determine what verification processes we need to maintain product quality.
NT: Recently, requirements vary by country, which adds another level of complexity. We've even changed package labeling to meet European regulations. Sometimes we need to switch out materials that were previously cleared. Maintaining a stable supply requires constant adaption, which can be challenging.
YI: That's why it's important to ensure we can source raw materials from multiple suppliers, and think about how to maintain product performance and quality while fulfilling our supply responsibilities.
- What initiatives are you pursuing on the production side?
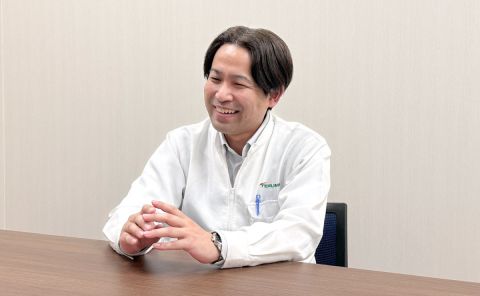
DM: In production, we've focused on improving the yield rate. Until around 2012, we produced everything at the Ashitaka Factory, so securing production volumes was our primary concern. Even then, we knew we had to improve the quality of each individual guidewire.
We examined every point where the wire contacted equipment during production, addressing issues one by one through equipment improvements. To monitor the effect of improvement, we sampled products at various stages to check their condition, then examined subsequent processes. We repeated this cycle continuously.
Our yield wasn't low to begin with, but we were still able to achieve significantly higher levels. It took about four to five years to finally reach our current yield rate, and now we can maintain stable production at those high levels.
This experience and knowledge proved valuable when we expanded production. When transferring part of the production to our second factory in Japan, their team members came to Ashitaka Factory to collaborate on improvement initiatives. Sharing our expertise meant that once the transfer of manufacturing was complete, they could achieve excellent yield rates from the outset at the new location.
- Quality is one of Terumo's core values, and it’s one of the reasons RADIFOCUS™ Guide Wire M continues to be chosen. How do you maintain consistent quality?
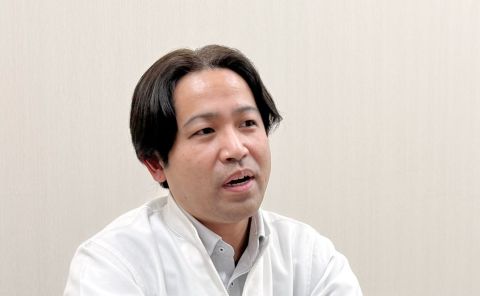
DM: Even though guidewires are relatively simple products, we need to work hard as a team to ensure consistency in outer diameter, coating condition, and tip shape every time. Coating is particularly important because it's not visible to the naked eye, and maintaining equipment parameters and condition through proper management is essential. You might assume that after 40 years of producing the guidewire, we’d have all new equipment. But because the product doesn’t change, we also need to maintain our equipment to match it. In fact, some machines have been maintained and used for over 30 years.
There are certainly challenges in preserving and producing something that doesn't change, but that's exactly what makes this work rewarding.
- What initiatives are you working on in development?
YI: As well as maintaining the current product, we’re continuously considering how to improve our materials. When we look at improving materials, it’s often about creating something more environmentally friendly and better for patients, rather than simply enhancing performance.
Improving materials do help us meet regulatory requirements, but those regulations exist because of what people need, so ultimately, these improvements benefit the end users.
NT: In every aspect of our job, not just improving materials, what really matters is whether we can confidently feel good about using these products with our own families.
- Selecting different materials while maintaining the same performance must be challenging.
YI: It is. Especially since these are used inside blood vessels. I think they’re among the most sensitive medical devices in the industry. That's why we need to conduct extensive testing beforehand and explore ways to prevent problems before they occur.
- It seems that each of you care deeply about the product. Would you agree?
DM: Yes, I would. When I joined Terumo, a senior colleague taught me to treat all products, not just guidewires, as if they were my loved ones. I’ve kept that mindset and passed it on, teaching new colleagues to treat each one carefully and gently. If you handle them roughly or knock them into something, they're easily damaged. They can get dented or punctured. Since these go inside the body, we're really careful about how we handle them.
NT: I approach my work by thinking carefully about what our customers expect, then try to deliver above and beyond that. It’s also important that with each feedback for improvement, we understand why they're coming to us and what their purpose is. Knowing that intent is the key to producing the best outcome.
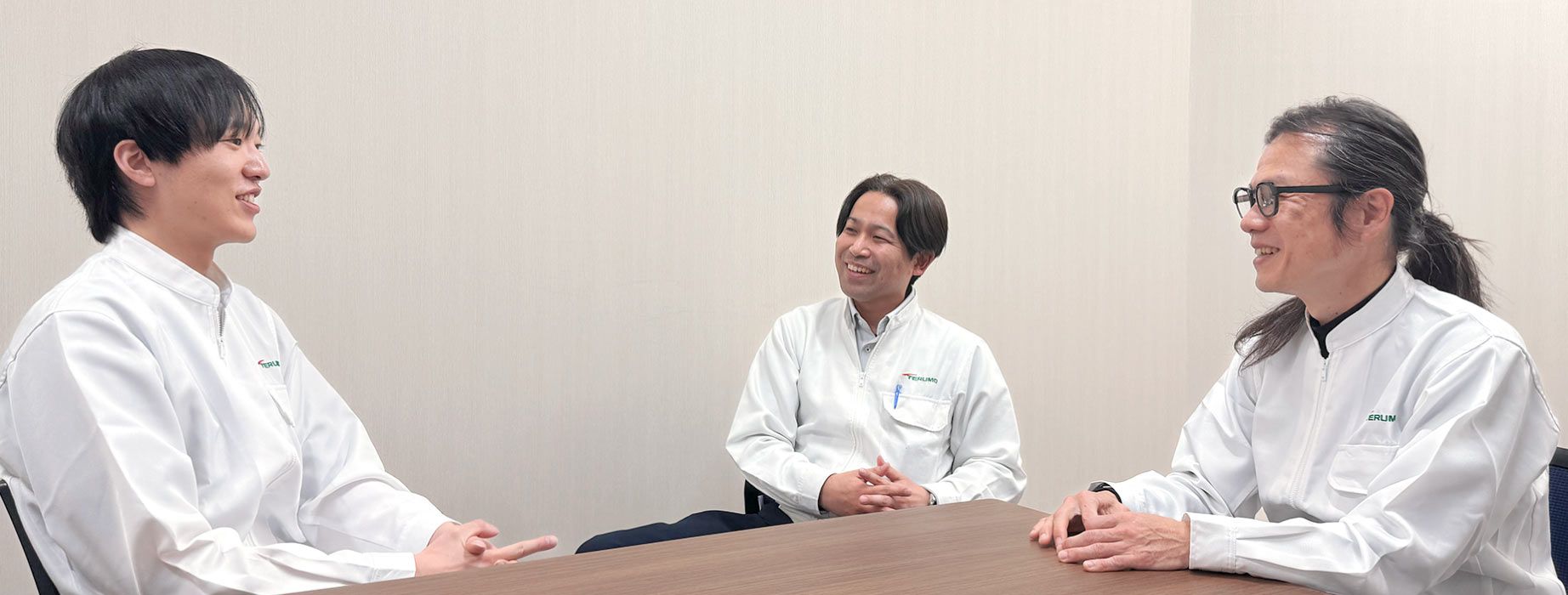
YI: Even though I’m in a different position from healthcare professionals, we share the same perspective of wanting to improve clinical practice and support it.
I also think it's important to constantly consider what the ideal should be for the product. We need to stay focused on the essential purpose: achieving real benefits for users and patients.
Being in development means we can analyze user feedback, and reflect our findings into our products. Which is why it’s important not to lose sight of that essential purpose of ensuring benefits for users and patients.
At the same time, it's not enough for development to simply want to make improvements. We also need to properly consider the production perspective and whether our improvements will actually enable stable production.
- What would you like to work on going forward?
For a better quality
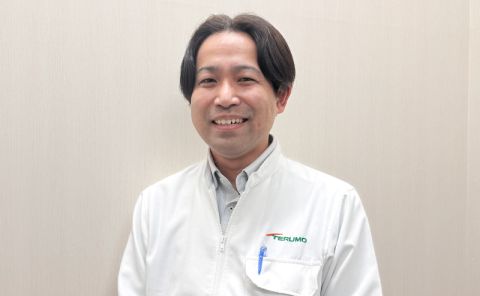
To the next generation
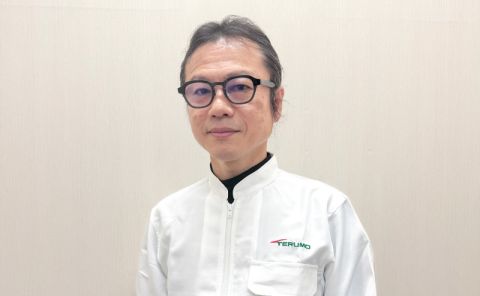
Go beyond what we have now
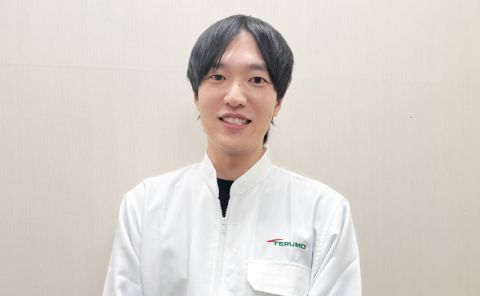
*Information accurate as of January 2025.